无内定位的小尺寸板外型尺寸精度改善研究
编者按:无内定位孔的PCB锣板因受力的影响,PCB加工至收刀处出现较明显的凸点,影响尺寸,凸点需100%人工修刮或研磨,导致生产效率低、修理良率低、外观、尺寸不良等问题。本文针对无内定位孔PCB锣板工艺进行深入研究、实验、批量生产验证,找出一种高精度、高品质、高效率的PCB锣板制作工艺。
③采用关闭吸尘的方法对凸点有较大程度的改善,但粉尘大,清洁耗费时间;
④采用“胶带固定法”所加工的品质明显优于其他三种方案,尺寸可满足客户要求。
3.2 “胶带固定法”工艺过程控制及要点
此种方法及文件设计未涉及到新物料、新设备,所以工艺过程管控和正常流程管控相同,包括外形尺寸、板边质量、凸点、毛刺等外观性的检验;过程实施需注意以下几点:
①无内定位的小尺寸PCB外形加工时,生产前板面需要双面贴胶膜(中性粘度PE胶膜),避免粉尘污染板面(特别是无法过清洗机的小板及金板),胶膜本身有一定粘度,可有效防止表面处理污染;
②“胶带固定法”实施流程图如图11所示;
③“胶带固定法”批量加工效果确认如图12~图14所示。
以上试验通过采用锣带优化,辅助过程中“胶带固定法”,有效避免了凸点的产生并降低了人工修理成本,优化后的加工工艺大幅提高了效率,以下方面仍存在改善空间:
。①过程中每加工一排产品需要贴一条胶带,胶带两端粘贴不牢固时,有移动风险,每次贴胶带均需要停机;
②无内定位产品尺寸较小,此加工方法成型后的产品,成品检查前需一块一块地撕去表面的保护胶膜,撕胶膜效率低,大批量加工时(图15),撕保护膜需要耗费大量的人工资源(图16)。
综合以上试验成果,锣带优化结合过程中的贴胶带固定的方式使产品在收刀位有固定力的作用,可解决无内定位产品收刀位凸点问题,批量加工外形尺寸可以控制在0.1mm以内,优化后的加工工艺大幅提高了效率,针对成型后的撕去保护表面处理的胶膜效率低的问题,需要寻找更好的处理方式,解决撕胶膜效率低的问题,具体优化后加工方式如下:
锣带优化,先锣每单元产品的部分区域,保证每单元部分区域先外形加工后仍有连接,再采用“贴胶膜+环氧树脂盖板固定法”利用胶膜的粘附力,辅助环氧树脂盖板,防止吸尘力的作用,保证产品铣至收刀位时,仍能够保证产品位置的固定,预防凸点问题,其流程图如图17所示。
4 结论
采用“贴胶膜+环氧树脂盖板固定法”能有效地避免无内定位产品外形凸点的产生,杜绝了修理带来的外观不良、尺寸不符等;采用外形前贴胶膜,外形后采用整体撕胶膜的方式除去保护表面处理的胶膜,解决了小尺寸产品外形加工后无法过成品机清洗的问题。此加工方式成型后的产品可免清洗,同时节省了人工,实现了无内定位产品高精度、高品质、高效率的加工。此方法未涉及到高成本的新物料、新设备,是对现有资源充分、合理的利用得出的成果,适用于批量加工高精度无内定的产品。
参考文献:
[1]林金堵,龚永林.现代印制电路基础[M].上海:印制电路行业协会,2001.
本文来源于威廉希尔 官网app 2017年第2期第70页,欢迎您写论文时引用,并注明出处。
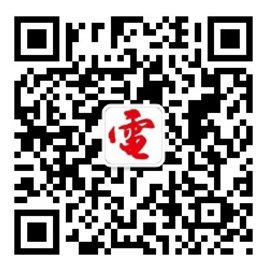
加入微信
获取电子行业最新资讯
搜索微信公众号:EEPW
或用微信扫描左侧二维码