洗煤厂集中自动化控制系统设计
2.2 洗煤厂控制工作原理
现场的控制和运行状态信号经三个PLC从站进行数据采集和变换,通过RS 485网送到上位工控机进行显示,工控机根据系统的运行状态发出控制指令。由于三个PLC从站实际上是并联连接,因此它们之间的数据是通过上位机发出的指令进行传送的。
2.3 洗煤厂控制系统硬件组成
FX2N是三菱FX系列PLC家族中最先进、性价比最高的一种,其突出优点是包容了标准特性,程序执行更快且全面补充和完善了通信功能,具有满足单个需要的大量特殊功能模块,最大控制点数高达256点,为自动化控制提供了最大的灵活性和控制能力。
在网络和通信方面,FX2N系统采用世界上最流行的开放式网络CC-Link,Profibus和DeviceNet以及RS 232,RS 422或RS 485串行通信,可组成传输高达12 Mb/s的控制网络。
采用三菱FX2N系列PLC及其串行通信转换接口FX-485PC-IF与研华工控上位机组成分布式集中控制系统,如图1所示。
其设计要点为:由于上位机为RS 232通信接口,而PLC为RS 485接口,必须通过通信转换接口FX485PC-IF进行转换;由于上位机主站到最末的3号PLC从站的实际距离为400 m左右,而FX2N系列PLC的RS 485通信板所构成的网路最大传输距离为50 m,因此在每台PLC从站上要用三菱通信适配器FX-485-ADP替换RS 485通信板,使上位机主站到最末一级的PLC从站的实际通信距离达到500 m,以满足现场设计的要求。
为增强系统的抗干扰能力,三个PLC从站对现场采集的数字量输入信号和PLC数字量输出信号均经过继电器隔离,模拟量信号的传输均采用屏蔽电缆;采用二台上位工控机,通过转换板使之互为备用,二台工控机运行相同的程序和画面。
2.4 洗煤厂控制系统软件设计
系统软件主要由PLC编程软件和上位机监控软件两部分组成。PLC编程软件使用专门开发的用于FX系列的FX-PCS/Windows 9X编程环境,可用梯形图、指令表或时序功能图进行编程;监控软件采用三维科技的Force Control(力控),此软件可方便地创建Windows操作系统下丰富的人机界面/监控与数据采集(HMI/SCADA)应用系统。
现场侧点信号由三个PLC从站采集后,通过RS 485网络送至IPC进行显示;煤仓中的煤位、水池中的水位等调节量和报警设定值在IPC操作后,结果通过RS 485网络送至相应的PLC。
IPC运行三维的Force Control软件,通过软件本身的实时数据(DB)和I/O驱动程序,建立起DB与I/O驱动程序的服务器/客户计算模式,I/O驱动程序完成过程I/O数据的采集与回送,三个PLC从站分别与三个I/O驱动程序相连。PLC之间的数据传递可通过创建脚本程序,并通过IPC发出指令来完成。
系统采用三维科技的Force Control 2.0工控组态软件进行画面的显示设计。Force Control有三种获得数据的方法:使用系统本身提供的I/O驱动程序、用户开发动态数据库DLL和使用动态数据交换DDB。由于系统本身具有FX系列PLC的I/O驱动程序,因此,以使用I/O驱动程序最为方便。数据显示方法有:模拟表显示、棒图显示、趋势图显示和历史曲线显示等。根据工艺和操作要求进行画面的分类设计,如整个洗煤厂的运行状态图,主洗厂房、水泵站和装车房的分画面,以及故障报警画面等。
3 结语
通过PLC应用实践,首先明确PLC控制系统要达到的目标。以提高生产率,增强控制的准确性为目的时,着重考虑与计算机的通信能力;其次,明确PC系统的结构方式,根据不同的控制对象选择相应的方式,比如对单台机床的控制选独立式即可;设备密集控制复杂的系统采用集中式为宜(如加热炉系统);分布式系统则宜于设备分散、局部系统独立性较强的系统;再次,系统设计时硬件和软件应综合考虑,二者不要绝对分开,因为,软件本身的硬件更具有修改的便捷性,且就二者的相互适应性而言,软件的可塑性绝对高于硬件;最后,系统运行后已完善的控制软件要坚信其正确性和可靠性,系统故障时应从硬件及外部设备的检查入手,不应轻易修改程序。
本文的洗煤厂集控系统,采用分布式集中控制的方法进行设计,具有可靠性高、使用方便、研制周期短和节约投资等特点。系统自投运以来,运行良好,对提高洗煤厂自动化水平和节约投资起到了良好的示范作用。
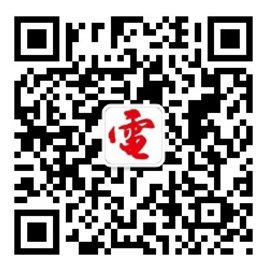
加入微信
获取电子行业最新资讯
搜索微信公众号:EEPW
或用微信扫描左侧二维码