MEMS的“CMOS化”成长
在6寸晶圆上,目前DRIE的刻蚀速率大约为30-50μm/min。根据Yole Development的预测,未来的发展趋势是多腔刻蚀,并在未来2-3年内达到大约100μm/min的刻蚀速率,同时减少昂贵的C4F8用量。Tegal的市场副总裁Paul Werbaneth认为,新兴的MEMS领域,如3D MEMS(即MEMS与MEMS或MEMS与CMOS逻辑芯片叠加在一起),在很大程度上依赖于DRIE来实现其最终的制造。市场的需求推动着DRIE技术向前发展,与CMOS的发展轨迹类似,向更大尺寸的晶圆发展会是趋势之一。Tegal未来的发展计划中就包括与客户一起进行300mm DRIE机台的开发。
MEMS的特点是三维加工,除需要进行同平面的光刻外,还需要对硅片正反面进行图形对准。双面光刻也由此而来。早期的双面光刻技术利用红外线可以穿透硅片却能被空气和金属吸收的特点进行双面对准。但红外线波长较长,对细线条的对准存在困难。此外,复杂的金属布线和不平整的表面对红外线的吸收将产生干扰。如今的双面光刻技术是基于光学对准的,对准精度有很大提高。
MEMS制造中,对于光刻的主要要求有:大聚焦深度和厚光刻胶的曝光;相对结构尺寸而言,极其严格的CD控制;用于衬底双面处理的双面校准工艺;在高深宽比结构情况下的大聚焦-校准偏移;对大面积器件进行曝光时具有良好的接缝和对接控制;材料处理(小晶圆,甚至是材料片)的灵活性。目前大多数MEMS产品使用的是传统的接触式光刻机,产品线宽为2-5μm。根据Yole Development的报告,现有的步进式光刻设备可以使MEMS的线宽达到0.6μm,套准精度约为20nm。因为MEMS器件的形貌相比CMOS而言要求更高,所以未来MEMS光刻设备主要需要解决的问题就是更小的尺寸,特别是DOF问题。随着线宽和套准精度要求的提高,光刻机从接触式曝光向DUV转变将是MEMS光刻工艺发展的方向。
MEMS与CMOS的集成
MEMS器件研究的发展和应用领域的拓宽推动着集成制造工艺的进步。器件研究与集成工艺的关系一般分为两类:一类是根据不同器件开发相应的工艺方案,另一类是在器件设计时尽量选择已经成型的标准工艺方案。从MEMS的量产和走入市场的角度来说,显然第二种选择更为明智。虽然向成熟工艺靠拢会使器件的设计受到一定的限制,但因为无需开发新工艺,设计好的器件可以在CMOS等成熟的生产线上生产。
对于标准集成方案,能否与CMOS集成电路兼容是在不同工艺方案间取舍的重要参考指标。一般来说,与CMOS集成电路兼容的工艺方案可以实现MEMS器件与信号控制电路的单片集成,可以在提高器件性能的同时降低总的加工成本。根据MEMS工艺与CMOS工艺的顺序不同,集成方案可分为Pre-CMOS、Intra-CMOS和Post-CMOS,即MEMS工艺在CMOS之前、中间或之后完成。从成本的角度考虑,CMOS之后完成MEMS是首选方案。因为在代工厂完成标准的CMOS电路,所制备的电路性能有所保证,而且成本也较低。
目前比较主流的Post-CMOS集成方法是表面牺牲层工艺,它可以制备较薄的MEMS结构,通常厚度为0.2-150微米。图3是表面牺牲刻蚀法制备薄型MEMS的示意图。该方法是指通过在衬底表面淀积不同的薄膜并结合选择性刻蚀得到悬浮微结构的过程。以氧化硅为牺牲层的多晶硅表面牺牲层工艺是此类工艺的代表。
SiO2或多晶硅表面牺牲层淀积以后,通过光刻和刻蚀步骤定义出所需结构,最后去除残余的牺牲层。SUSS MicroTec中国区总经理龚里博士介绍说,MEMS制造中的两个关键问题就是应力和温度。表面牺牲层工艺的结构层和牺牲层多采用CVD和PVD方法制备,所制备的薄膜通常会有较大的残余应力。因此,优化工艺参数以减小残余应力是保证其性能的关键。此外,由于金属铝不能承受多晶硅的淀积温度,所以标准的多晶硅表面工艺无法实现Post-CMOS集成。所以,与电路集成时一般要先完成低温多晶硅结构的制备。也可以利用金属钨代替铝做金属连线,或者用多晶的锗硅做结构材料。
“CMOS与MEMS器件相结合是未来发展的大趋势,”Paul Werbaneth说,“它可以融合MEMS与CMOS器件的功能,实现芯片的多功能性,未来的市场发展也相当乐观。”
MEMS如何与传统代工厂相融合?
图4从各个方面分析了MEMS的现状与未来发展趋势。显而易见,就是设计的可制造性、生产的标准化、CMOS-MEMS的片上系统(SoC)集成、8寸生产线、占领市场时间的缩短以及成本的降低。
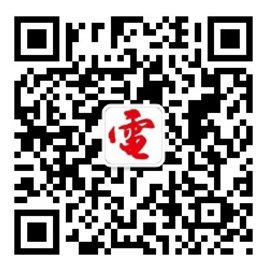
加入微信
获取电子行业最新资讯
搜索微信公众号:EEPW
或用微信扫描左侧二维码